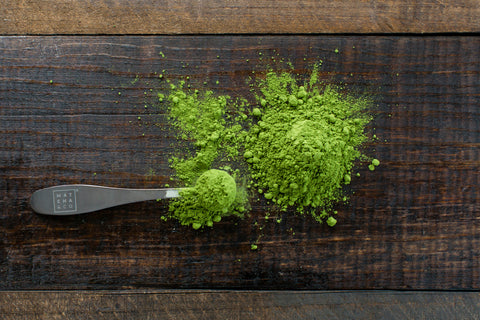
In the dynamic world of nutraceuticals, powder supplements have gained immense popularity due to their convenience, versatility, and enhanced absorption rates. Powder manufacturing plays a pivotal role in the creation of these sought-after nutritional formulations. Summit Rx is a full-service contract powder manufacturer and packager. This blog will delve into the intricacies of powder manufacturing in the nutraceutical industry, exploring key processes, considerations, and the role of powder supplement technology in delivering high-quality products.
Understanding Powder Manufacturing in Nutraceuticals
From the global nutritional supplements market size valued at US $337 billion in 2022, the powder formulations segment generated a market share of 37%. Here are the main steps involved in powder supplement manufacturing,
- Raw Material Selection:
Powder manufacturing begins with the careful selection of raw materials. Nutraceutical formulations often include vitamins, minerals, amino acids, and herbal extracts. High-quality ingredients are essential for producing effective and safe powder supplements.
Example: A reputable powder supplement manufacturer meticulously sources organic and non-GMO raw materials to ensure the purity and potency of their products.
- Blending and Mixing:
Once the raw materials are obtained, they undergo precise blending and mixing. This step ensures uniform distribution of ingredients, minimizing variations in each dosage.
Example: Powder supplement manufacturers employ advanced mixing technologies, such as ribbon blenders or fluidized bed mixers, to achieve homogeneity in their formulations.
- Granulation:
Granulation involves the formation of granules from powder blends to improve flowability, compressibility, and stability. This step is crucial for creating cohesive and easily compressible powders. Using our in-house powder manufacturing services, Summit Rx can help increase or decrease the particle size through dry granulation for obtaining capsules with the required amount of dosage.
Example: Nutraceutical powder manufacturers may use wet or dry granulation techniques, depending on the specific characteristics of the ingredients and the desired end product.
- Tablet Compression or Capsule Filling:
Powder supplements are commonly consumed in tablet or capsule form. Tablet compression involves compacting the granulated powder into tablet form, while capsule filling involves encapsulating the powder.
Example: Powder supplement manufacturers invest in state-of-the-art tablet compression machines or capsule filling equipment to ensure precise dosages and consistent product quality.
- Quality Control:
Rigorous quality control measures are implemented throughout the manufacturing process. This includes testing raw materials, in-process samples, and finished products to meet regulatory standards and ensure product efficacy. We take pride in manufacturing supplements without or minimal use of excipients and making the final product with a “ clean label” tag.
Example: A reputable powder supplement manufacturer conducts thorough tests for potency, purity, and contaminants, employing third-party laboratories for independent verification.
- Packaging:
Proper packaging is crucial to preserve the stability and shelf life of powder supplements. Packaging materials should be moisture-resistant and protect against light to maintain the product's integrity. Summit Rx provides both private and white label packaging options along with bringing your products to life.
Example: Leading powder supplement manufacturers invest in eco-friendly and airtight packaging solutions, ensuring that consumers receive products with optimal freshness and potency.
Roller Compactor, Fermentor and Fluid Bed Dryers
The process of manufacturing powder supplements involves several specialized equipment and technologies to ensure the quality and efficacy of the final product. Here's how roller compactors, fermentors, and fluid bed dryers play crucial roles in the production of high-quality powder supplements,
- Roller Compactor:
Roller compactors are instrumental in the granulation phase of powder supplement manufacturing. This equipment is designed to transform fine powder blends into compacted sheets or ribbons, which are then milled into granules. The granulation process enhances the flowability and compressibility of the powder, facilitating the subsequent steps of tablet compression or capsule filling. Learn how roller compaction can help with efficient powder manufacturing.
Example: A protein powder blend undergoes roller compaction to form granules, ensuring uniform distribution of ingredients and optimal compactability for tablet formation.
- Fermentor:
Fermentors are commonly used in the production of certain types of powder supplements, especially those containing probiotics, enzymes, or other bioactive compounds produced through fermentation. Fermentation is a controlled process where microorganisms metabolize specific substrates, leading to the production of desired compounds.
Example: A powder supplement containing probiotics is manufactured using a fermentor, allowing the beneficial bacteria to proliferate and produce bioactive compounds beneficial for gut health.
- Fluid Bed Dryers:
After granulation or fermentation, the powder may contain excess moisture that needs to be removed to ensure stability and prevent microbial growth. Fluid bed dryers are used to efficiently remove moisture from granulated or fermented powder by passing heated air through the product bed, promoting drying and maintaining the powder's desired characteristics.
Example: Granules formed in the roller compactor are subjected to fluid bed drying to eliminate moisture, ensuring the stability and extended shelf life of the powder supplement.
Benefits of Powder Manufacturing Technologies
These technologies contribute significantly to the overall quality and efficiency of the powder supplement manufacturing process. Here are the benefits of using powder manufacturing technologies,
- Consistency in Particle Size:
Roller compactors aid in achieving consistent particle size by controlling the compression force applied during the compaction process. This ensures uniformity in the final product, enhancing the blend's homogeneity.
- Enhanced Bioavailability:
The controlled environment of a fermentor allows for the production of bioactive compounds, such as probiotics and enzymes, which may have increased bioavailability compared to their synthetic counterparts.
- Efficient Drying:
Fluid bed dryers provide an efficient and controlled drying process. The adjustable parameters, such as air velocity and temperature, allow manufacturers to tailor the drying conditions to the specific requirements of the powder supplement, preventing degradation of sensitive ingredients.
- Optimized Formulation:
By utilizing these advanced technologies, powder supplement manufacturers can optimize the formulation to meet the desired characteristics, including texture, density, and moisture content. We take pride in our 47,000 sq.ft. state-of-the-art manufacturing and packaging facilities, which enable us to produce affordable custom high-quality powders.
In conclusion, roller compactors, fermentors, and fluid bed dryers play integral roles in ensuring the efficiency, quality, and stability of powder supplements. The integration of these technologies in the manufacturing process contributes to the production of high-quality powder supplements that meet the stringent standards of the nutraceutical industry. Request a free quote today and let’s discuss your powder manufacturing needs. We also take on small R & D projects and would love to contribute to growing your brand!